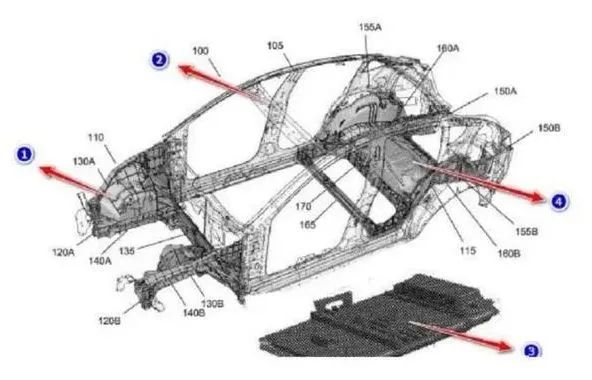
在电池PACK结构简化的过程中,不同结构与材料的增加或减少使用以及传统结构件在生产供应的格局上均发生较大变迁。

图:CTP电池包结构下各生产环节增量与产业迁移梳理
PART 01
结构件:电池托盘的生产工艺变化
冲压→挤压/压铸:
当期挤压将代替冲压,远期压铸正在局部尝试
铝挤压工艺相比于传统的冲压等生产工艺,具有高刚性、抗震动、抗挤压、抗冲击等性能。
但是:①铝型材的焊接工序很长,效率很低,一体化压铸快速成型,效率更高;
②型材焊接的焊缝质量问题,一体化压铸可较好的解决。
③从生产成本的角度,无需投资多种铝型材的设备,一体压铸仅需一台压铸设备,整体工艺生产流程简化。

图:铝合金电池托盘
PART 02
CTC 后底盘开启一体化压铸新纪元
特斯拉引领汽车制造工艺创新极简,开启一体化压铸新纪元
2020年9月,特斯拉于电池日上宣布Model Y将采用一体化压铸后地板总成,可减少下车体总成重量30%,降低40%制造成本,且车身生产工艺流程大幅简化,制造时间由传统冲压-焊装-涂装-总装制造工艺的1-2小时缩短至一体化压铸的2-3分钟。
2021年5月,特斯拉前舱一体化总成铸件试验也已披露下线,主要构成包括左右车轮罩、溃缩吸能区、横梁、以及与车身连接的端面和与前碰撞梁或车前端连接的结构端面,整体重量约为130kg。
当前,特斯拉正在探索一体化压铸的进一步集成,将整个车辆的结构构成大大简化为四个部分:
①前舱一体式压铸总成+②乘员舱结构压铸总成+③一体化电池结构压铸总成+④后底板一体化压铸总成。

图:新能源车车身结构简化与集成
其中,据特斯拉发布会介绍,其利用3个大型压铸件(前底板+CTC电池包+后底板)替换由370个零件组成的整个下车体总成,实现整体减重10%,续航增加14%。
一体化压铸是汽车制造提升集成效率,以及轻量化与降成本必经之路
1
一体化压铸相对传统工艺,极大的提升了汽车车身的生产效率
传统车身的制造工艺包括冲压-焊装-涂装-总装等多个流程。主车厂采购由全国各供应商通过冲压、压铸制造的多个结构件,将之组装连接(包括焊接、铆接、涂胶 等)在一起,形成汽车的白车身总成(BIW)。一辆车由大约几百个不同形状、不同材料的零件焊接而成。任一零件的误差波动都将对最终的车身精度造成影响。

图:一体化压铸极大提升了汽车生产效率
一体化总成零部件一次压铸成型,极大提升了汽车生产效率与集成质量。据特斯拉数据显示采用了一体式压铸后地板总成的Model Y,由于所有零件一次压铸成型, 零件数量比Model3减少79个,由于应用了新的免热处理合金材料,因此省去了热处理环节,制造时间由传统工艺的1-2小时缩减至 120-180s。且只有一个零件,无需开发过多的工装设备,也大幅降低大量零件连接带来的误差累计,提升制造精度。
2
一体化压铸有效实现了汽车轻量化需求
据中国汽车工程学会给出的国内汽车轻量化分阶段目标来看,国内汽车制造轻量化趋势也在不断加速推进。采用铝合金一体化压铸的全铝白车身重量约在200- 250kg,而同级别钢制车身的重量在350-450kg。重量降低约 150-200kg,采用全铝一体化压铸工艺极大的提升了汽车的轻量化程度。
3
一体化压铸大幅简化生产成本
一方面,大幅降低了生产线成本。在原有的有生产技术成本(冲压、焊装、涂 装、总装)框架下,传统生产70个零部件,每个零部件均需布置机器和模具,以及生产线周边的机器臂、传输线、夹具等;而一体化压铸成型仅需一台大型压铸机和一套模具,工艺流程简化过后其它耗材和设备的减少、机加工简化、物料运输、压铸成本都更小;且省去了热处理设备和过程、省去了塑型设备[修复热处理后的变形]和过程、省去了钝化设备和过程、省去了结构胶等,综合经济性能更好。另外,一台大型压铸机占地面积仅100平方米,根据埃隆-马斯克的表示,采用大型压铸机后,工 厂占地面积减少了30%。
另一方面,大幅降低人力成本。国内主流汽车工厂一个焊装工厂大概配套200- 300名生产线工人,采用一体压铸技术后,所需的技术工人也将大幅减少。据特斯拉在2020年电池日发布会上表示,modelY后底板一体化压铸工艺较原方案降低了40% 制造成本。
主车厂与电池厂均跟进,加速布局新能源车底盘一体化压铸项目,行业景气高增
1
各新能源车厂加速跟进推进一体化压铸
沃尔沃布局一体化压铸:2022年2月28日,沃尔沃汽车将投资100亿瑞典克朗给位于瑞典的Torslanda 制造工厂,以准备生产的下一代全电动汽车。公司将采用大型铸造铝车身部件,新建电池组装厂和总装车间。其中关键一项是使用 8000T 锁模力的巨型压铸机生产汽车后底板,这意味着沃尔沃开始在大型汽车零部件中引入压铸工艺。

图:沃尔沃布局CTC压铸
新势力造车企业携手第三方,开始布局一体化车身压铸。除特斯拉外,新势力造车企业如蔚来、小鹏等也开始布局汽车的一体化压铸后底板。2021年12月蔚来发布新车 ET5,该车后座板使用一体压铸工艺。
2
电池厂商宁德时代深度
布局电池包结构压铸
2021年8月,宁德时代与上海临港签订合作协议,拟投资28亿元建设一体化电动底盘项目。2022年2月19日基地正式开工。项目涉及布局包括先进材料、系统结构、 极限制造和商业模式创新在内的“四大创新体系”。
3
压铸厂商亦高度受益行业景气高增,
单车价值量大幅提升,市场空间广阔
除车厂采购压铸机自研一体化压铸后底盘外,车身结构件的压铸厂商以及电池包和电驱动壳体的压铸厂商同样进行着一体化压铸业务的布局。在当前新能源车销量高增以及大型压铸件使用不断扩张背景下,零部件厂商高度受益压铸件需求放量。

图:一体化压铸极大提升了汽车的生产效率
4
一体化压铸对设备-模具-工艺配套流程要求
更高,技术壁垒明显,竞争格局更优
一体化压铸“设备-模具-材料-工艺”集成综合壁垒高
在设备端,大型一体化成型件需要采用高吨位压铸机,当前国内外各压铸机设备厂商开始实现大型压铸机研制突破。为了满足大尺寸部件的制造要求,且同时保证其强度和量产效率,一体化压铸对压铸机的锁模力、模板尺寸、压射量、压射压力以及速度控制等均需要更高的要求,具有较高的技术难度。各主车厂及第三方压铸厂纷纷采购超大吨位压铸机来实现业务拓展布局。
在模具端,大型压铸产品结构复杂,对模具的要求亦进一步增加。在材料端,免热处理合金材料的研制突破助力大型一体化压铸的适用推广。传统压铸工艺中,需要使用到热处理等工序来提高零部件的机械性能、耐腐蚀性能等。但加热冷却过程中产生的热胀冷缩效应,带来零部件的形变误差,特别是对于一体化的大体积部件,进一步放大了变形风险。
在压铸工艺端,将设备-模具-材料大要素有机地加以综合运用在当前仍具备较高 的技术壁垒,其关键点在于能稳定的、有节奏的和高效的生产出外观、内在质量好、 尺寸符合要求的合格铸件。
同样,樱花扎根中国20年,金属压铸脱模应用在各领域,在这次一体化压铸的工艺变化过程中,樱花积极参与,从2500T到9000T的压铸机台都能见到樱花各种最新型号的脱模产品。高配比的脱模产品进一步帮助制造企业降低工耗,提高良品率,最大程度上优化了部件成本,提高了效率。





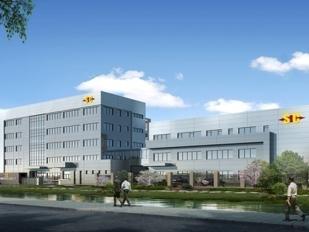



欢迎合作伙伴来电咨询相关产品信息
电话:021-64953666
END